AC MACHINES-1 (66761) Theory
14. Realize the principle of starting of a 3-phase induction motor.
14.2. List the starters used for starting 3-phase induction motor.
Necessity of Starter
The three phase induction motors are self-starting due to rotating magnetic field. But the motors show tendency to draw very high current at the time of starting. Such a current can be 6 to 8 times of full load or rated current and it can damage the motor winding. Hence there should be a device which can limit such high starting current. Such a device which limits high starting current is called a starter.
Let us study in detail why starter is required for an induction motor.
- In a 3 phase induction motor, the magnitude of an induced emf in the rotor circuit depends on the slip of the induction motor. Thus induced emf effectively decides the magnitude of the rotor current. The rotor current in the running condition is given by :
I2r = s E’2 / (R22 + sX22)
- At starting time, the speed of the motor is zero and slip is at its maximum i.e. unity. So magnitude of rotor induced emf is very large at start. As rotor conductors are short-circuited, the large induced emf circulates very high current through rotor at start.
- The condition is exact similar to a transformer with short-circuited secondary. Such a transformer when excited by a rated voltage, circulates a very high current through short-circuited secondary. As secondary current is large ⇒ Primary current also draws very large current from the supply line.
- Similarly in a 3 phase induction motor, when rotor current is high, consequently the stator draws a very high current from the supply line. Due to such increment in line current ⇒ Voltage starts deeping. ⇒ Whole system can collapse. ⇒ Hence even 3 hp rating induction motor is not allowed without Starter.
List the starters used for starting 3-phase induction motor.
Starting methods of Induction motor include:
- Direct –On– line (DOL) starters for less than 10 Kw motors.
- Star–Delta starters for large motors. The stator winding is initially connected in a star configuration and later on changed over to a Delta connection, when the motor reaches rated speed.
- Auto transformer. There are three main methods of Starting of Cage Induction Motor. They are as follows.
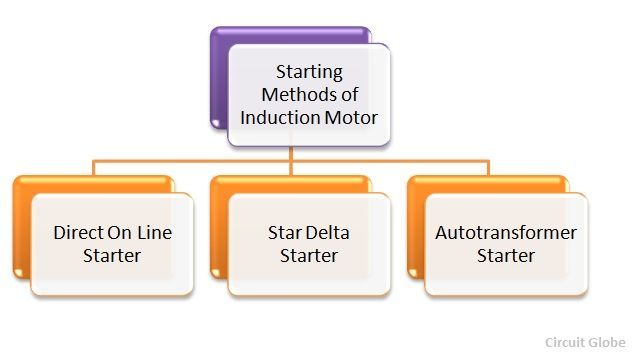
Direct on line starter
The direct on line starter method, of an induction motor is simple and economical. In this method, the starter is connected directly to supply voltage. By this method small motors up to 5 kW rating is started to avoid the supply voltage fluctuation.
Star delta starter
The star delta starter method of starting three phase induction motors is very common and widely used among all the methods. In this method, the motor runs at delta connected stator windings.
Auto transformer starter
The Auto transformer is used in both the type of the connections, i.e., either star connected or delta connected. The auto transformer is used to limit the starting current of the induction motor.
The above three starters are used for cage rotor induction motor.
Slip Ring Induction Motor Starter Method of Starting Induction Motor
In the Slip Ring Induction Motor starter, the full supply voltage is connected across the starter. The connection diagram of the slip ring starter induction motor is shown below.
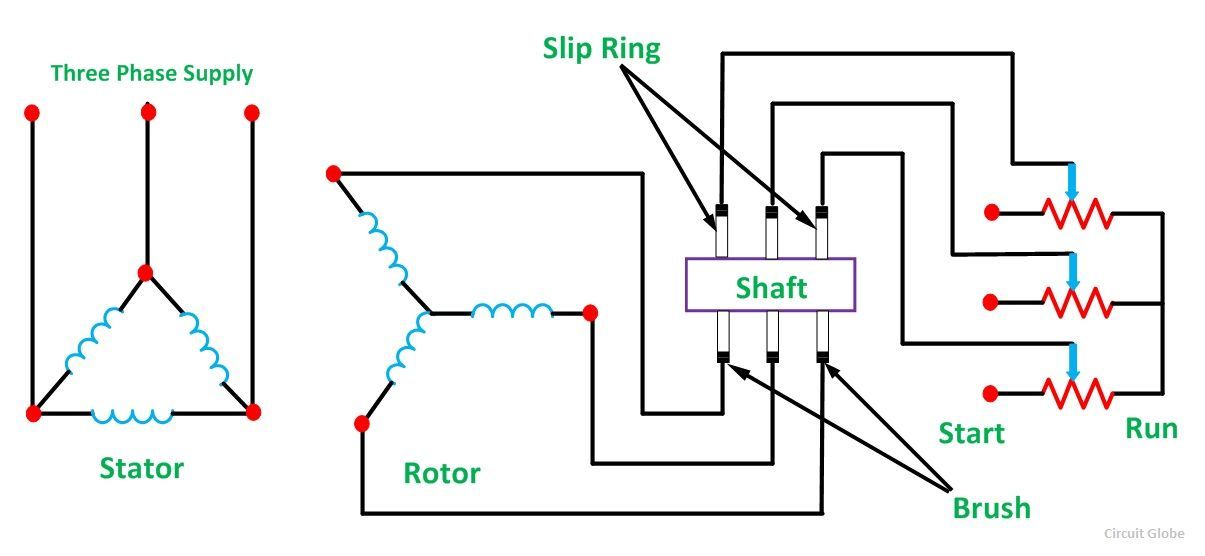
Full starting resistance is connected and thus the supply current to the stator is reduced. The rotor begins to rotate, and the rotor resistances are gradually cut out as the speed of the motor increases. When the motor is running at its rated full load speed, the starting resistances are cut out completely, and the slip rings are short-circuited.